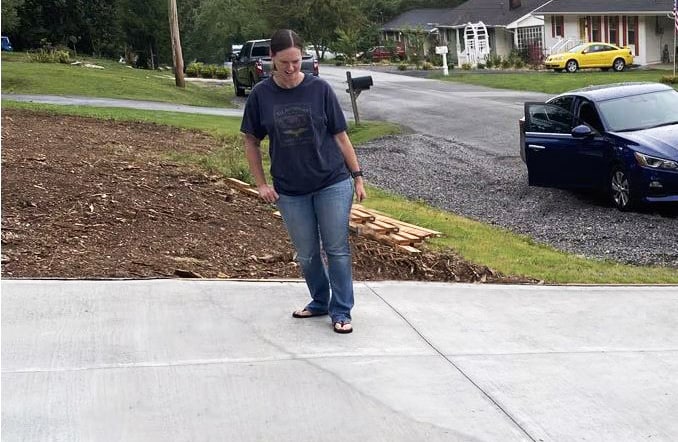
Your project is finally over—that beautiful new concrete slab is finished. You replant the grass, start using it with your family… and then you see it. A crack. You’re certain it wasn’t there when the concrete company finished the job. But it’s only been a few months (or a few days), and now you feel angry because clearly the company screwed up. Right?
Not so fast. Sure, there are plenty of ways to mess up a concrete job, especially when you don’t use an experienced concrete contractor. But the reality is, CONCRETE CRACKS. Good, new concrete that’s properly installed… still cracks. Unfortunately, even the best concrete companies have to regularly field complaint calls from customers over cracking. As a concrete slab settles, small, hairline cracks will start to appear (sometimes immediately!).
“There are only two kinds of concrete driveways: those with cracks, and those that haven’t cracked yet,” one contractor “cracked” in a homebuilder forum I saw online. Another chimed in, “If someone asked me to pour a concrete driveway and guarantee there wouldn’t be hairline cracks, I’d run away screaming.”
When installed properly, concrete is one of the longest-lasting, most durable building products you can use around your home. But most homeowners don’t understand that concrete cracks are common and anticipated. The customer expects concrete to behave like other materials, where breaks only occur when it’s old or poorly constructed.
Quality Built Exteriors owner Mike Reedy told me that while his company uses all the best practices and materials for their concrete work, they nevertheless receive irate calls. So he is now devoting more time to educating customers, to help them go into a concrete project with realistic expectations.
Reasons why concrete cracks
Shrinkage
There are many possible reasons that cracks can develop in concrete. When new concrete cracks, the most common culprit is shrinkage—a completely normal development that has nothing to do with structure or durability.
Concrete is made from cement, which is a mixture containing water so that the material is “liquid” enough to flow and mold into the desired shape. Water is also necessary for concrete to properly cure, through a chemical process called hydration. As the concrete cures, excess water evaporates—which causes the volume of the concrete to shrink and pull apart from itself, leading to the development of small cracks. Adding control or expansion joints when pouring the slab is one tactic contractors use to help control where the cracking takes place, so it’s not as unsightly.
Improper site prep or installation
It’s critical for concrete contractors to follow well-established guidelines with respect to cement mixing and placement. Strong, crack-resistant concrete does not happen by accident.
Too much water in the mix (usually done to make installation easier and cheaper) will cause more severe cracks—in higher quantities. Cement poured on frozen soil, non-compacted ground, or on an area that hasn’t been properly prepared and graded, will also lead to cracking.
Pressure, weight, settling and expansion
There are plenty of other, more obvious reasons concrete can crack. Tree roots can push up on it, the ground can naturally settle beneath it or something extremely heavy could be placed on top of it. These issues often take time to develop visible cracks and are typically noticed several months to years after installation.
What’s the “cure?”
An ounce of prevention
To minimize the number and severity of cracks, choose a reputable concrete contractor. This professional will make sure the optimal mix is poured onto a properly prepared surface. It can be more expensive to have it done right, as it takes more manpower to pour stiffer mixes on well-prepared ground. But, in this case, the old adage rings true: “You get what you pay for.”
A pound of perspective
To prevent disappointment in your new concrete slab, enter the project expecting small, shallow cracks. If a larger crack does occur, approach your contractor to discuss your concerns (nicely!). Together, you and the contractor can examine the severity of the crack, repair options and expected outcomes.
While superficial fissures can be patched, often the “fix” is more unsightly than the crack itself. Getting an exact color match to the original concrete is nearly impossible. The color of concrete fades over time and is dependent on the elements at the time of mixing and the conditions when it was poured.
A ton of proactiveness
All that said, if cracks in your slab are wider than 1/8” or continue to widen over time, don’t look the other way—you may have a more serious structural issue. Larger cracks allow water to reach the rebar below (though some concrete projects are done without needing rebar), which can rust the steel. The water can also freeze and put pressure on the solid surface. Both issues eventually lead to more significant and problematic cracks in your concrete.
Should you notice larger cracks, reach out to your installation company right away, especially if it is still under warranty (check the original contract). If not, call a professional concrete contractor like Quality Built Exteriors to take a look in-person and assess your remediation options.
For experienced and professional help with your next concrete project or repair, contact Quality Built Exteriors.